Projekt jest na bardzo wstępnym etapie realizacji.
Wykonane próby jedynie potwierdzają słuszność przyjętej metody.
Wszelkie wymiary są wzięte z sufitu, zapewne należy je skorygować.
Kilka słów wstępu.
Ostrząc wiertło kręte należy zachować symetrię ostrzy, właściwe kąty i odpowiednie zatoczenie.
O ile wiertło naostrzone niesymetrycznie i pod katem różnym od 120 stopni będzie wiercić, co najwyżej rozbije otwór na większy wymiar, o tyle niewłaściwe zatoczenie skutkuje tym, że albo wiertło nie wejdzie w materiał, albo szybko się stępi.
Najprościej by było wiertło umieścić wewnątrz nagwintowanej z wierzchu rury wkręcanej w nakrętkę umieszczoną pod odpowiednim kątem do ściernicy, niestety tak da się naostrzyć tylko pół wiertła, żeby naostrzyć drugie ostrze trzeba by cofnąć nakrętkę o pół gwintu. Są jeszcze inne powody dla których nikt nie stosuje tej metody, ale dobrze ona oddaje aspekt teoretyczny.
Tak więc ostrzenie wiertła polega w istocie na zsynchronizowanym obracaniu i przybliżaniu/oddalaniu wiertła od ściernicy.
Sporo czasu kombinowałem nad automatyczną ostrzarką, najlepiej CNC, ale wszystkie projekty były zbyt skomplikowane i zwyczajnie zbyt drogie.
Aż w końcu zadałem sobie pytanie : po jasną cholerę kupiłem drukarkę 3D ?
Aczkolwiek jestem zwolennikiem tezy, że wydruk 3D z zasady nie nadaje się do niczego, to ma jednak niewątpliwą zaletę, że da się nim zrobić elementy niewykonalne żadną inną metodą. Na przykład można wywiercić otwór o prostokątnym przekroju, do którego z żadnej strony nie da się podejść żadnym narzędziem... Po prostu takie cuda, jakie tylko w komputerze da się wymodelować.
Tak więc padło na oś obrotową i krzywkę.
Oś obrotowa, bo ma być tanio, krzywka jako element wymienny, który daje się łatwo wymodelować i szybko wydrukować.
Pierwsze wydruki poszły do śmieci, bo dla "oszczędności" wydrukowałem je na pięćdziesiąt procent wypełnienia. Połamały mi się w rękach. Drugi komplet drukowany na 100% wyszedł lepiej, chociaż i tak jeden element pękł tam gdzie się można było spodziewać. Tym razem w ruch poszła "Kropelka" ...
Zasadniczo warto pamiętać, że wydruk 3D trzeba traktować jak szkło - wytrzymuje spore ściskanie, ale małe rozciąganie może skutkować pęknięciem. Najlepiej tam gdzie i tak ma pęknąć rozciąć i dać śrubę ...
Pierwszy prototyp wygląda tak :
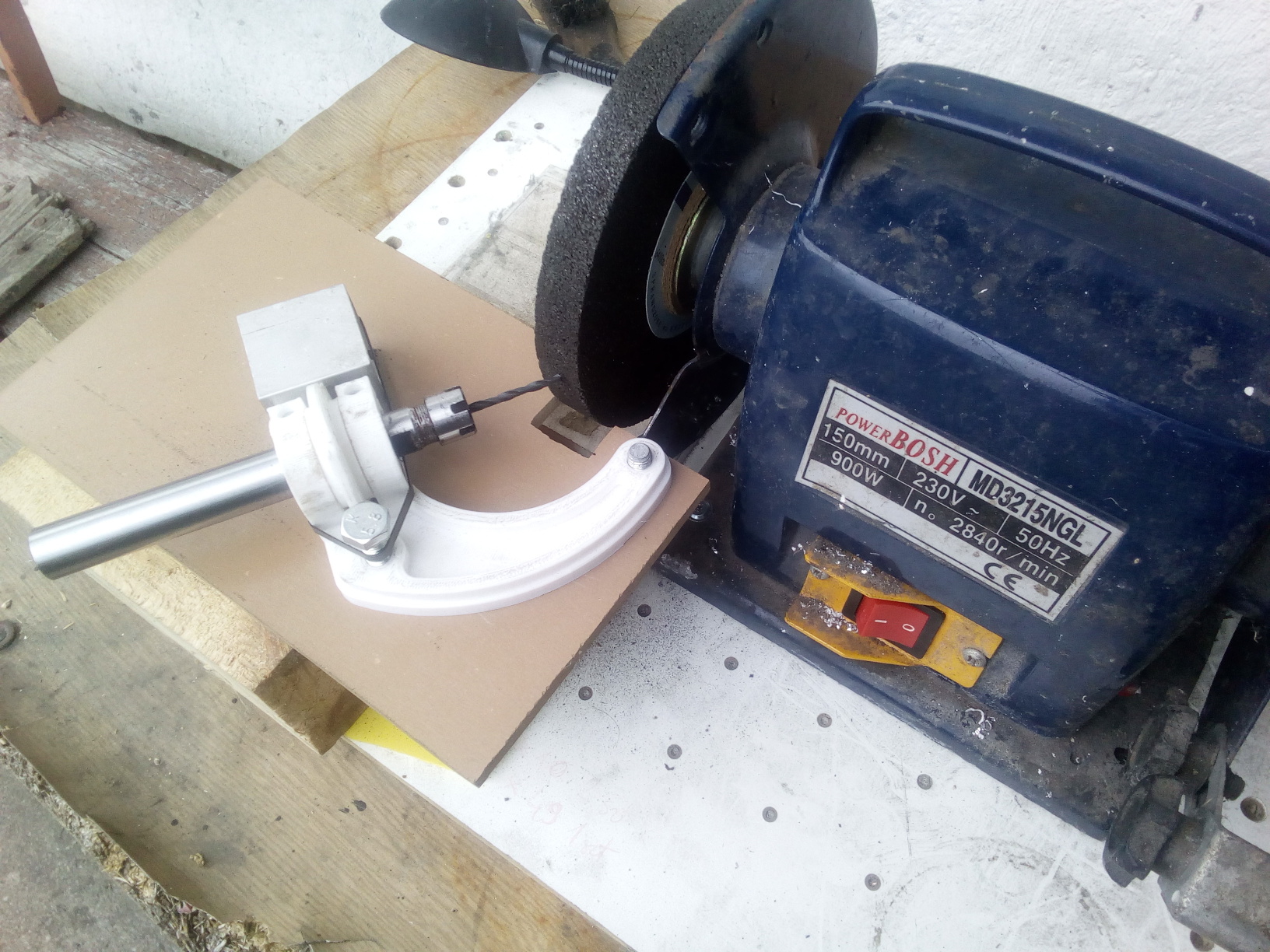
Urządzenie składa się z płyty (tutaj kawałek panela podłogowego), uchwytu wiertła (tutaj ER11 na wałku ⌀16, miałem to użyłem), wydrukowanej bazy obracanej na kołku (oś obrotu jest blisko ściernicy), zderzaka (tutaj kawałek aluminiowego profila, bo mi się nie chciało rzeźbić), krzywki (kiepsko widać, ale to jest to pomiędzy dwiema obejmami co dotyka zderzaka), kołka (tutaj za kołek robi śruba M8, bo miałem pod ręką) i sprężyny (tutaj gumka "recepturka" czyli pierścień odcięty z dętki rowerowej).
Całość obraca się wokół osi blisko ściernicy i jest dociągana sprężyną (gumką) do zderzaka.
Krzywka jest zamocowana TYLKO na wałku uchwytu wkrętem M3. Luzując wkręt można wsuwać/wysuwać wałek i obracać krzywkę względem wałka. Krzywka wchodzi bez luzu pomiędzy obejmy bazy, więc dociśnięcie wkręta jednoznacznie bazuje wiertło.
Sprężyna dociąga wiertło do ściernicy, ale tylko tyle ile pozwoli krzywka. Tak więc wraz z obrotem wiertło przybliża się lub oddala od ściernicy, zgodnie z zarysem krzywki.
Krzywka ma oczywiście dwie symetryczne połówki, które z kolei dzielą się na dwa fragmenty, które nazwałem "dosuw" i "odskok". "Dosuw" to część odpowiedzialna za zatoczenie ostrza, "odskok" jak nazwa wskazuje, to szybkie oddalenie wiertła przed obróbką drugiego ostrza.
Ustawienie wiertła do ostrzenia planuję na zasadzie opisanej w wątku ustawianie-offsetu-i-wysokosci-noza-mik ... 05567.html czyli kamerą w odpowiednim uchwycie, ale tego jeszcze nie zrobiłem, bo się machnąłem z wymiarami i się nie dało tak ustawić kamery żeby patrzyła centralnie na wiertło.
Ma to tak wyglądać, że bazę będzie się zdejmować z płyty przy szlifierce (szlifowanie w pobliżu kamery to głupi pomysł) i zakładać na płytę pomiarową w której będą trzy otwory/kołki bazujące bazę jednoznacznie a kamerę obrotowo.
Ma to wyglądać jakoś tak :
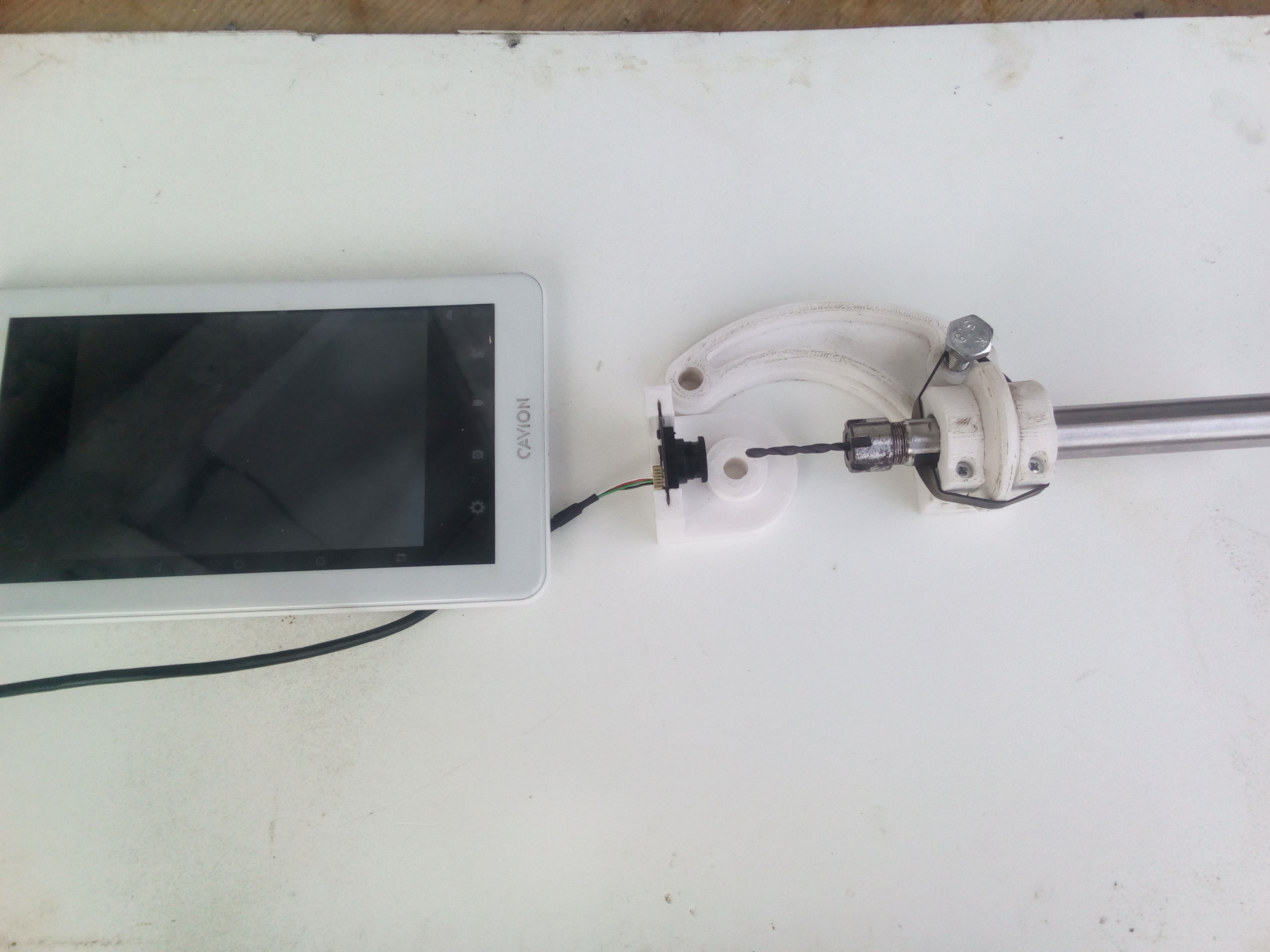
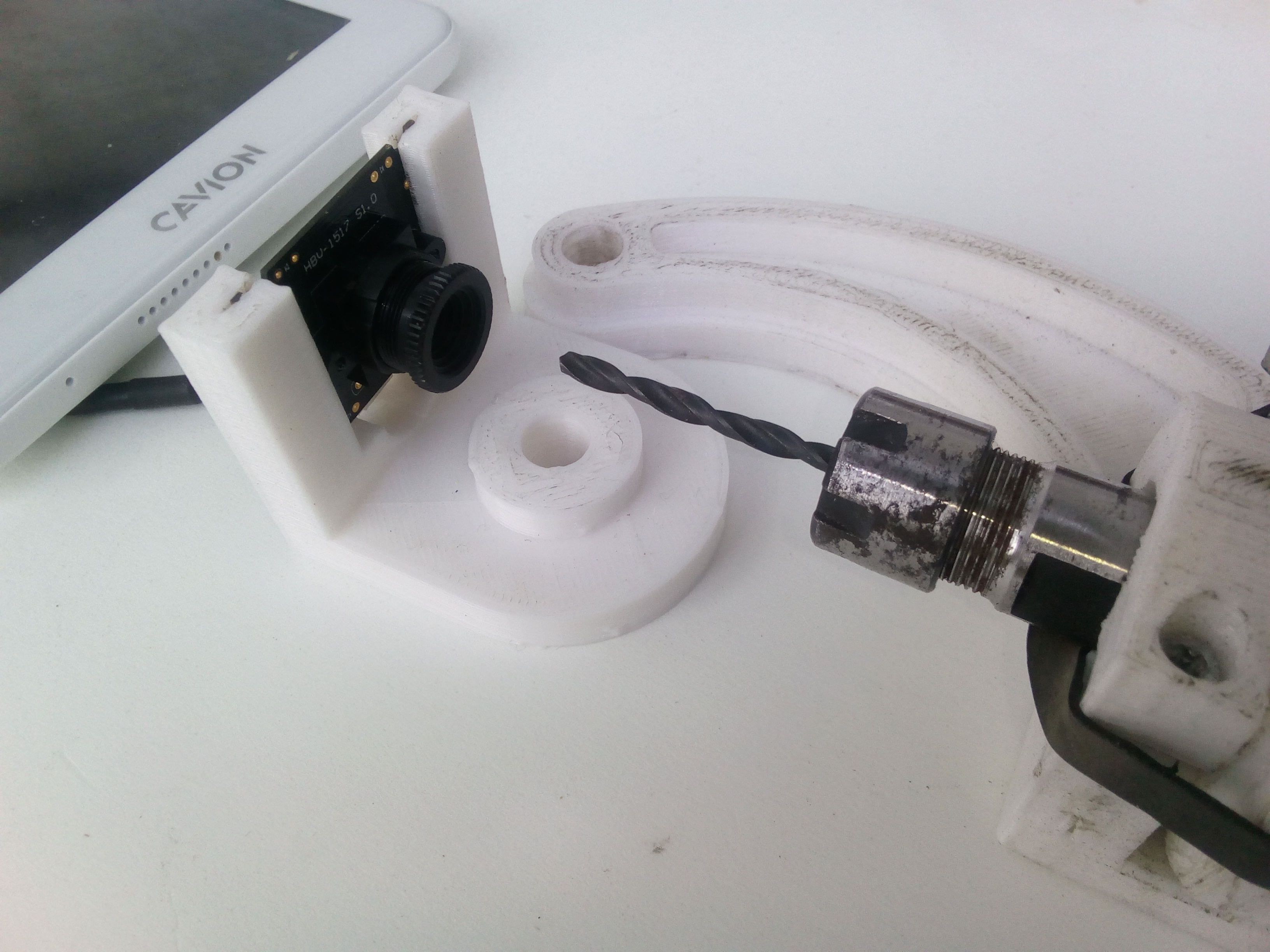
Tutaj jeszcze jedna fotka, centralnie widać krzywkę, niestety nie pomyślałem przy robieniu zdjęcia i "robaczek" ustalający jest pod spodem. Ten "robaczek" ma jeszcze jedną funkcję, mianowicie jest znacznikiem ustalającym położenie krzywki względem wiertła. Czyli jeśli na kamerze wiertło ustawimy względem krzyża, to robaczek musi być w określonym położeniu względem pionu i poziomu (znacznika na bazie).
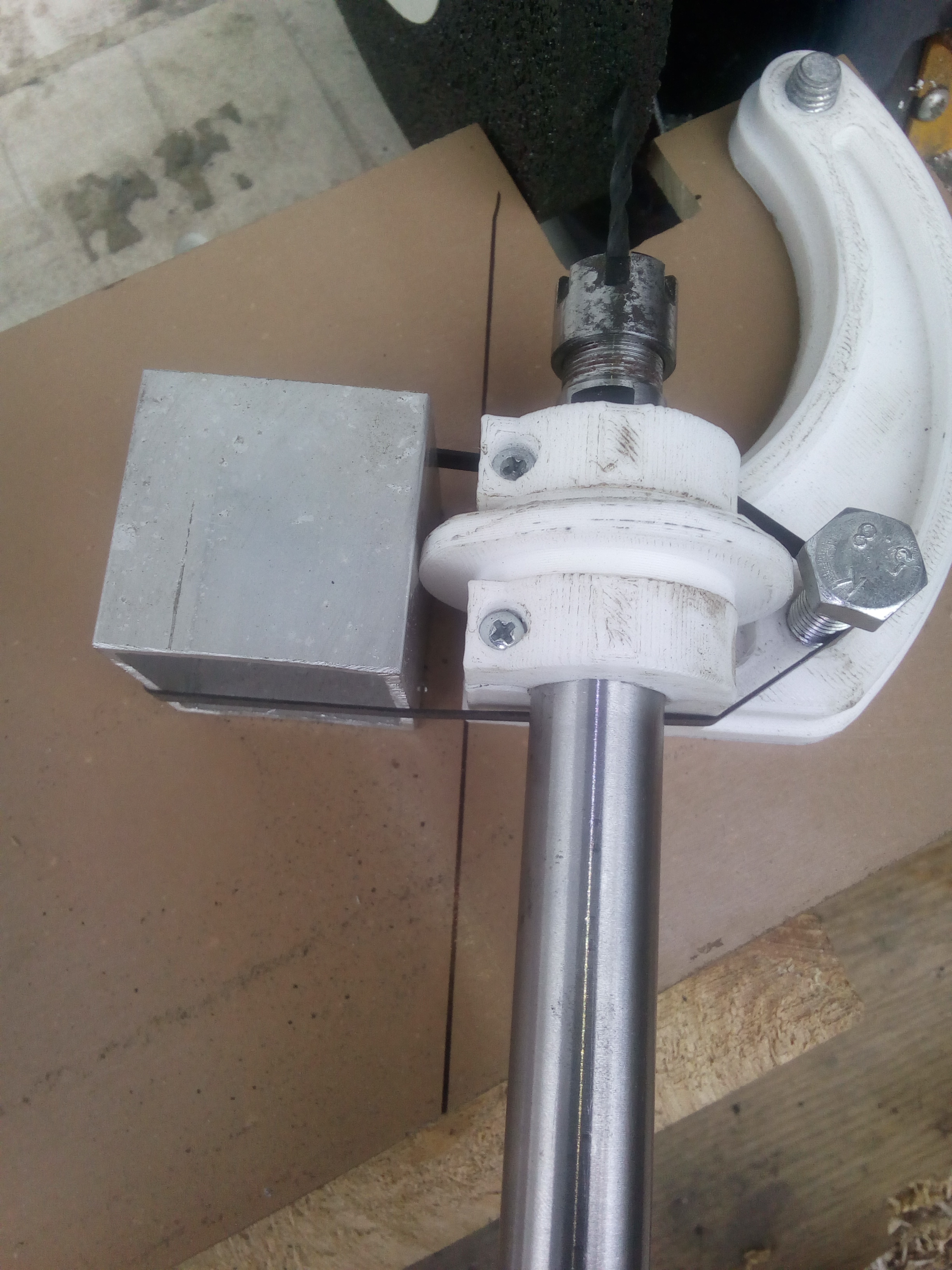
Załączam pliki w OpenScad i STL. Jak pisałem, mocowanie kamery jest za szerokie, ale pewnie i tak nikt nie ma akurat takiej kamerki, więc ten element i tak będzie musiał przeprojektować.
Podobnie zresztą z uchwytem wiertła, może być dowolny na tulejki czy szczękowy, byleby na cylindrycznym chwycie, dającym się przesuwać względem obejm i krzywki.
Pewnie dla różnych wierteł trzeba będzie użyć innych krzywek.
No i nakrętka M3 nie chce wchodzić w gniazdo w krzywce, musiałem trochę poddłubać i nabić młotkiem, będę to musiał poprawić, ale dzisiaj już nie dam rady.
TERAZ NAJWAŻNIEJSZE.
Ustawiając wiertło ⌀3mm "na czuja" udało mi się je dość poprawnie naostrzyć.
Do ideału daleko, ale wykonałem próbne wiercenia w drewnie, aluminium i nierdzewce, czyli dość paskudnych materiałach i szło jak w maśle.
Znaczy to tyle, że pomysł jest dobry, trzeba tylko dopracować szczegóły.